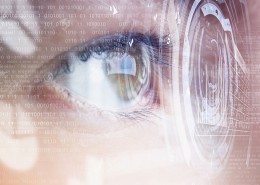
© Olha Rohulya
LNG bietet eine attraktive, günstige und vor allem umweltschonende Alternative zu herkömmlichen Treibstoffen in der Schifffahrt. Jedoch können in der LNG-Kette ab dem Terminal bis zur Verbrennung im Motor klimarelevante Emissionen entstehen. Insbesondere dem Entweichen von Methan (der Hauptkomponente von LNG) kommt dabei eine besondere Rolle zu, und zwar nicht nur durch Leckagen, sondern durch den „Methanschlupf“ gewisser Anlagenkomponenten der Gasmotoren. Das Problem besteht nicht nur in einem Verlust an nutzbarer Energie, sondern vor allem darin, dass Methan in der Atmosphäre eine sehr starke Treibhausgaswirkung hat.
Daher müssen Emissionen von unverbranntem Methan im Sinne des Klimaschutzes in den LNG- Schiffsantriebsanlagen so weit wie möglich verhindert werden. Vorteile im Hinblick auf die Umweltbelastung, die sich aus der Nutzung von LNG im Vergleich zu herkömmlichen Kraftstoffen für die Schifffahrt ergeben, können durch eine unvollständige Verbrennung von Methan in den Gasmotoren somit wieder reduziert oder sogar zunichte gemacht werden.
Budget
Arbeitstunden
Projektpartner
Das Ziel, Schiffsmotorenanlagen zu entwickeln, die kein bzw. kaum Methan im Abgas freisetzen, soll durch den Einsatz von Katalysatoren erreicht werden. Diese Katalysatoren haben die Aufgabe, das restliche Methan im Abgas in Kohlendioxid und Wasser umzuwandeln. In dem Katalysator müssen dazu die geeigneten Bedingungen (z.B. Temperaturen, Drücke, usw.) zum vollständigen Ablauf dieser chemischen Reaktionen bereitgestellt werden.
Gestützt durch Erfahrungen mit Rußfiltersystemen für Dieselmotoren, die bereits erfolgreich mit der Technologie „thermische Regeneration“ arbeiten, soll auch bei Katalysatoren zur Methanoxidation der Prozess durch Zuführung von Wärme, unter Benutzung des für den Motor vorhandenen Brennstoffs, initiiert werden.
Projektpartner
Bei der Realisierung des Systems sollen folgende Komponenten berücksichtigt werden:
- Bestimmung des Energiebedarfs (Wärme).
- Bestimmung der erforderlichen Komponenten und der Systemkonfiguration, Brennerleistung, Mischkammer, Katalysatorformulierung.
- Dimensionierung der Komponenten.
- Durchführung von CFD Simulationen.
- Produktion der Prototyp-Komponenten und Konfiguration.
- Entwurf und Bau eines Basiskontrollsystems.
- Umfangreiche Testphase
- Verarbeitung der gesammelten Daten und Berichterstattung